Are you looking to improve the quality of your construction projects? Implementing quality assurance and control measures is the key to ensuring that your projects meet the highest standards. By following a systematic approach, you can minimize errors, reduce costs, and deliver exceptional results. In this guide, we will explore the importance of quality assurance and the key components of quality control measures. You will learn how to conduct regular inspections, perform quality testing, and maintain detailed documentation. By implementing these measures, you will not only enhance the overall quality of your construction projects but also build a reputation for excellence in the industry. So, let’s dive in and discover how you can successfully implement quality assurance and control measures in construction.
Key Takeaways
- Continuous improvement enhances efficiency, reduces waste, and optimizes project performance.
- Training and education ensure workers stay updated on industry standards and best practices.
- Implementing regular inspections helps identify potential hazards and take immediate corrective actions.
- Documentation and record-keeping throughout the construction process facilitate transparency, regulatory compliance, and future reference.
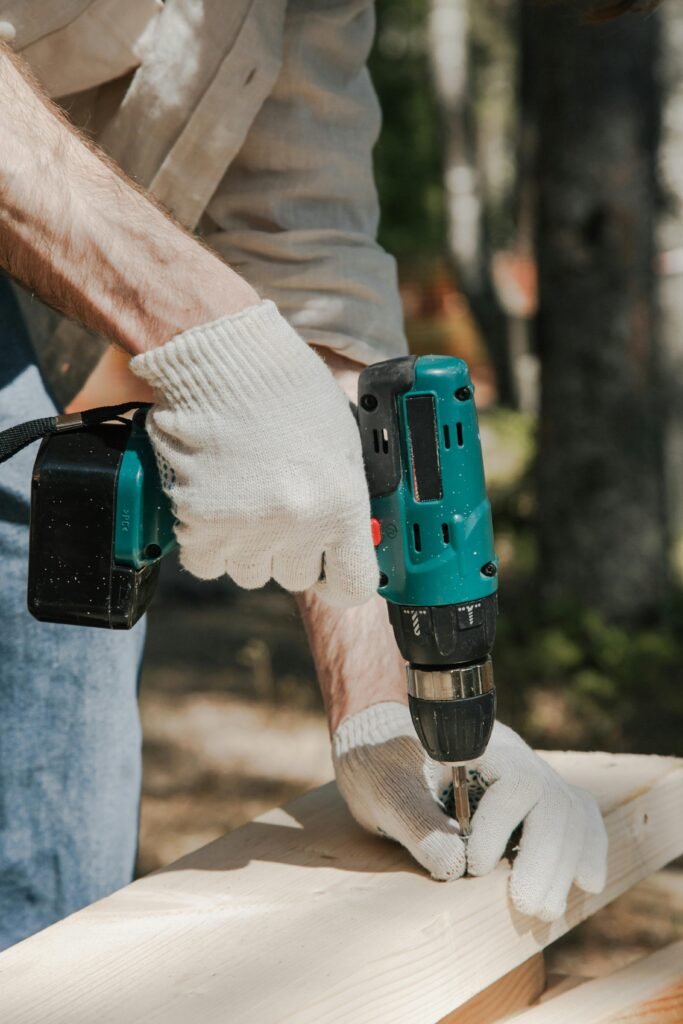
The Importance of Quality Assurance
Implementing quality assurance measures in construction is crucial for ensuring the delivery of a high-quality end product. Continuous improvement is an essential aspect of quality assurance in construction projects. It involves constantly analyzing and evaluating processes, identifying areas for improvement, and implementing necessary changes. By adopting a mindset of continuous improvement, construction teams can enhance efficiency, reduce waste, and optimize overall project performance.
Training and education play a vital role in quality assurance. Construction industry professionals must undergo regular training to stay updated on the latest industry standards, best practices, and technological advancements. Through training programs, workers can acquire new skills and knowledge, enabling them to execute their tasks more effectively and efficiently. This, in turn, contributes to the overall quality of the construction project.
Additionally, training and education help ensure that all team members are aware of quality assurance protocols and procedures. By having a shared understanding of quality expectations, construction teams can work together cohesively and consistently deliver high-quality results.
Key Components of Quality Control Measures
What are the key components of quality control measures in construction, and how can they be effectively implemented? To ensure the highest standards of quality in construction projects, it is crucial to have robust quality control measures in place. Here are the key components that you should focus on and implement effectively:
- Quality Control Training: Provide comprehensive training programs to all personnel involved in the construction process. This includes educating them about quality standards, inspection techniques, and relevant regulations.
- Standard Operating Procedures: Develop and implement standardized procedures for quality control activities. These procedures should outline the specific steps and requirements for conducting inspections, testing materials, and addressing non-conformities.
- Documentation and Reporting: Establish a systematic documentation and reporting process to track quality control activities. This includes maintaining records of inspections, test results, and any corrective actions taken. Regular reporting allows for transparency and facilitates continuous improvement.
- Continuous Improvement: Encourage a culture of continuous improvement by regularly reviewing and analyzing quality control data. This involves identifying areas for improvement, implementing corrective actions, and monitoring the effectiveness of these measures.
Implementing Regular Inspections
To effectively implement regular inspections in construction, ensure that every team member understands their role and responsibilities. Regular inspections are crucial for identifying potential risks and ensuring that corrective actions are taken promptly. Conducting regular inspections allows you to assess the quality of work being done and identify any deviations from the project specifications or industry standards.
Start by developing a comprehensive inspection checklist that covers all aspects of the construction process, including structural integrity, safety measures, and compliance with regulations. Assign specific team members to conduct inspections at different stages of the project. Provide them with proper training and guidance on how to perform thorough inspections and document any issues or non-compliance.
During inspections, focus on risk assessment to identify potential hazards that could affect the project’s quality, safety, or timeline. This includes checking for structural weaknesses, inadequate safety measures, or deviations from approved plans. If any issues are identified, take immediate corrective actions to address them. Document all findings and actions taken to ensure accountability and traceability.
Conducting Quality Testing
Continue ensuring the quality of your construction project by conducting thorough quality testing throughout the process. Quality testing is essential to identify any defects or deficiencies in materials, workmanship, or design, and to ensure that the project meets the required standards and specifications. Here are some key quality control procedures that you should consider incorporating into your construction project:
- Non-destructive testing: This testing method allows you to evaluate the integrity of materials and structures without causing damage. Techniques such as ultrasonic testing, radiographic testing, and magnetic particle testing can be used to detect internal flaws or defects.
- Visual inspection: Visual inspection involves visually examining the construction components to identify any visible defects, such as cracks, uneven surfaces, or improper installations. Regular visual inspections should be conducted to catch any issues early on.
- Material testing: It is crucial to test the quality and properties of construction materials before using them in the project. This includes testing the strength, durability, composition, and other relevant characteristics of materials to ensure they meet the required standards.
- Performance testing: Performance testing involves verifying that the constructed elements and systems perform as intended. This may include load testing, water penetration testing, or fire resistance testing, depending on the project requirements.
Documentation and Record-Keeping
Maintain comprehensive documentation and record-keeping throughout the construction process to ensure transparency and accountability. Regulatory compliance and effective communication are key aspects of this process.
To achieve regulatory compliance, it is crucial to document all relevant information related to permits, licenses, and inspections. This documentation should include detailed records of any changes made to the original plans, as well as any deviations from the approved specifications. By keeping a record of these activities, you can demonstrate that you have followed all legal requirements and standards.
Effective communication is essential for successful construction projects. Documenting all communications, whether written or verbal, helps ensure that everyone involved is on the same page. This includes documenting discussions, decisions, and instructions given to subcontractors or suppliers. By maintaining a record of these communications, you can minimize misunderstandings, resolve disputes, and hold all parties accountable for their actions.
Comprehensive documentation and record-keeping also provide a valuable resource for future reference. It allows for the identification of trends, patterns, and lessons learned that can improve future projects. It also facilitates the sharing of information with stakeholders, such as clients, regulatory agencies, and auditors, ensuring transparency and building trust.

Frequently Asked Questions
What Are the Potential Consequences of Not Implementing Quality Assurance and Control Measures in Construction?
Without implementing quality assurance and control measures in construction, you risk potential consequences such as poor workmanship, safety hazards, project delays, increased costs, and client dissatisfaction. It is vital to prioritize quality assurance in construction projects.
How Can Quality Control Measures Help Prevent Future Construction Defects or Failures?
By implementing quality control measures, you can prevent future construction defects or failures. These measures ensure that materials and processes meet standards, leading to a higher quality outcome and reducing the risk of errors or failures.
Are There Any Industry Standards or Regulations That Dictate the Implementation of Quality Assurance and Control Measures in Construction?
Yes, there are industry standards and regulations that dictate the implementation of quality assurance and control measures in construction. These guidelines ensure that construction projects meet the required standards for safety and quality.
What Are Some Common Challenges or Obstacles That Can Arise When Implementing Quality Assurance and Control Measures in Construction?
When implementing quality assurance and control measures in construction, you may face construction challenges and quality control obstacles. These can include issues with compliance, coordination, communication, and resource allocation.
How Can Technology and Digital Tools Be Utilized to Enhance Quality Assurance and Control Measures in Construction Projects?
You can enhance quality assurance and control measures in construction projects by utilizing technology and digital tools. Benefits include improved efficiency and accuracy. However, challenges may arise in terms of implementation and training.
Conclusion
Implementing quality assurance and control measures in construction is vital for delivering exceptional results. At Cramer Rao Construction Ltd., we prioritize a comprehensive approach to quality management throughout every project phase. Our team establishes clear quality standards, conducts regular inspections, and utilizes industry best practices to ensure compliance. By fostering a culture of accountability and continuous improvement, we identify and address potential issues proactively. This commitment enhances project outcomes, reduces rework, and boosts client satisfaction. Contact us today to learn how our quality assurance and control measures can elevate your construction project and ensure outstanding results.